I know you are wondering, “What happens to all the scrap metal that Astro produces on a daily basis?” The answer is simple. We recycle it!
For scrap metal recycling, Astro Metal Craft partners with a company called Scrap Metal Processors. Their team comes out to take the scrap metal from our jobs. This comes off our lasers, water jet, punch, and the other fabrication tools that we use in the shop. Our full sheet sheet skeletons go onto a skid of all the same material type. It then gets loaded up into a roll off dumpster provided by Scrap Metal Processors.
A wide variety of metals are recyclable. Here are the two most common ones that come out of our shop:
- Aluminum: The poster child of metal recycling, aluminum is endlessly recycled into new cans, building materials, and even car parts.
- Steel: The world’s most recycled material, steel is used in everything from buildings to cars. Recycling steel conserves resources and reduces energy use.
As our jobs begin to accumulate smaller pieces of scrap, we put those pieces into a 4′ x 4′ metal bins. Again these are separated by material type. Once we have a bout 12 bins filled up, Scrap Metal Processors comes and we exchange them with more empty bins. They then take the metal to their processing plant for recycling.
The industrial metal recycling process is similar to any recycling program but has unique requirements related to sorting, preparation, and transportation. Our friends at Scrap Metal Processors walk us through their step by step process.
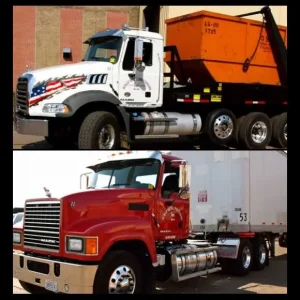
Stage 1. Collection & Transportation
First, pick-up and drop-off services are provided to companies like Astro that create a bulk amount of scrap metal. During this stage, the metal is collected and transported to their facility.
Stage 2. Identification & Sorting
The next stage requires the identification and sorting of scrap metal. Ferrous metals containing iron, which is magnetic, are separated from non-ferrous metals. Removal of non-recyclable materials is also required during the sorting process. We can only produce high-quality recycled metals by using high-quality source materials.
Stage 3. Compacting
Next, the metal needs to be compacted by a variety of machines to reduce the surface area to volume ratio, which means it will melt more effectively. Metals are shredded, squashed, broken, and squashed into tiny pieces or sheets.
Stage 4. Melting
Furnaces are used to melt metals, and each type of metal requires a large, specialized furnace. The sheets or pieces are poured in and heated to a specific melting temperature. This process can take minutes to hours depending on the volume of metal, amount of heat being applied, and the type of furnace or metal.
Next, the melted metals are purified to protect the final recycled product and the integrity of the products it will be used for in the future. Some examples of purification processes are electrolysis, the most common, or a magnetic system that removes foreign particles.
Stage 6. Solidification
Conveyor belts carry the molten metal to a cooling chamber for solidification. Chemicals may be added during this stage to alter certain properties such as density. During this process, metals can be shaped and sized, typically into bars or blocks that are easily transported.
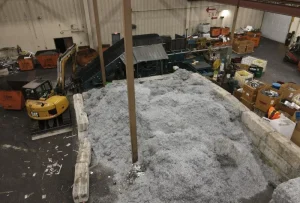
Stage 7. Export Transportation
Finally, the processed scrap metal is now recycled and prepared for use in manufacturing by a large variety of industries!
Pretty neat right?